Challenges and Strategies for Obsolete Technology
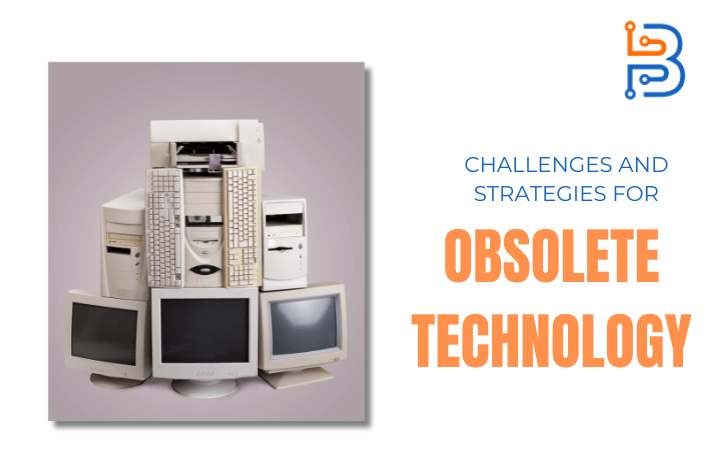
In order to stay competitive, manufacturers pursue innovation and concentrate on the newest technology. But as we move to the future, industry faces a paradox: a heavy reliance on obsolete technology. This paradox serves as the foundation for many important facets of manufacturing, such as maintaining production continuity and encouraging novel forms of innovation. We’ll examine the usefulness of obsolete technology today, along with a few obstacles and solutions.
Understanding the Obsolescence of Tech
Technological obsolescence is a multifaceted concept. At its core, it signifies the decline in usefulness or efficiency of a technology compared to newer alternatives. This decline can be driven by several factors:
- Advancements in Technology: The rapid pace of innovation often renders existing technology obsolete within a few short years. Newer hardware boasts increased processing power and functionality, while software advancements offer improved user interfaces and expanded features.
- Shifting User Needs: As user expectations and needs evolve, technology must adapt to remain relevant. For example, the rise of mobile devices has rendered traditional desktop applications less appealing for tasks requiring on-the-go accessibility.
- End-of-Life Support: Manufacturers eventually cease providing updates and support for older technologies. This lack of security patches and bug fixes exposes users to vulnerabilities and compatibility issues.
Read Also: 10+ Positive Impacts of Technology on Society
The Unseen Value of Obsolete Technology
1- Production Continuity
Many manufacturing processes still rely on equipment considered technologically obsolete. These machines, built to last, often continue to function effectively long after their supposed obsolescence. For specific production lines, the cost of replacing these machines with modern equivalents can be prohibitive, offering diminishing returns on investment. In such cases, the continued operation of older equipment ensures production continuity, maintaining output without incurring significant capital expenditure.
2- Specialized Applications
Obsolete technologies sometimes possess unique characteristics that are valuable for specialized applications. Certain manufacturing processes may require the specific capabilities of older machines that modern technology cannot replicate without considerable customization. In industries where precision and material handling of a particular nature are critical, such as in the production of specialized textiles or components, obsolete equipment becomes irreplaceable.
3- Knowledge Preservation and Innovation
The operation and maintenance of older technology serve as a conduit for knowledge transfer across generations. The skills required to operate, troubleshoot, and repair these machines embody a wealth of practical engineering knowledge.

Challenges with Obsolete Equipment
While there are many benefits to obsolete tech, there are of course many challenges with it.
1. Sourcing Issues
As equipment ages, manufacturers will regularly discontinue the production of certain parts making it increasingly difficult to maintain and upkeep them. Similarly, the number of people familiar with the tech will decrease over time. These factors combined often means manufactures have to scramble to source and to get parts repaired.
2. Incompatibility
Obviously obsolescence makes it a challenge for manufacturers to integrate modern software with older technologies. This leads to inefficiencies, unpredictable maintenance needs, and worst of all downtime on the production line.
3. Regulation And Safety Issues
As technology advances so do safety regulations to stay current with new challenges. This makes it difficult for manufacturers with older equipment to stay up to date with tregulations. Which can lead to unexpected fines and downtime.
Strategies for Dealing with Obsolescence
1. Developing a Replacement and Upgrade Strategy
Manufacturers should conduct regular assessments of their equipment inventory to determine which machines are critical to operations and which are candidates for replacement. Developing a phased replacement or upgrade strategy can help mitigate the impact on production and finances.
2. Sourcing and Stockpiling Spare Parts
Manufacturers should look at what critical tech and equipment they have and start sourcing and stockpiling spare parts now. The availability of these parts will only go down in the future so getting them before you need them is key.
3. Investing in Skills Development
Consider investing in training programs to keep newer employees informed on the functionality of older tech. Additionally, creating detailed documentation of equipment operation and maintenance procedures ensures that this knowledge is preserved within the organization.
4. Exploring Retrofitting and Custom Solutions
Retrofitting obsolete equipment with modern controls and connectivity can extend its useful life and integrate it into contemporary manufacturing systems. Custom engineering solutions can also address specific issues, such as improving safety features or reducing environmental impact.
Beyond Organizations: Individual Strategies
While the focus often lies on organizational challenges, individuals are equally susceptible to the pitfalls of obsolete technology. Here are some strategies individuals can adopt:
- Stay Informed: Remain updated on the latest technological advancements in your field or area of interest. This allows you to identify opportunities to leverage new tools and enhance your skills.
- Security Awareness: Prioritize security measures like strong passwords, regular software updates, and using reputable antivirus programs to protect your devices and data from cyberattacks.
- Software Subscriptions: Consider software subscriptions over one-time purchases. Subscription models often provide access to automatic updates and the latest features, ensuring you remain on the cutting edge.
- Embrace Open Source Alternatives: Explore open-source software options for common tasks. Open-source software is often free or considerably cheaper than commercial alternatives and benefits from constant community development.
Conclusion
The importance of obsolete technology in manufacturing extends beyond mere nostalgia or resistance to change. The preservation of priceless industrial knowledge, specialized applications, and production continuity all depend on these legacy systems. Even though integrating and maintaining outdated equipment might be difficult, strategic management can help by easing these problems and allowing firms to fully utilize their technological assets.
The thoughtful maintenance of outdated technology highlights a more general reality as the industrial industry develops: future innovation frequently has its roots in the past. Manufacturers may guarantee a balanced advancement in technology by recognizing the importance of outdated equipment and implementing techniques to manage it well. This allows the old and new to coexist and promote productivity, efficiency, and creativity.